Manhès–David-processen
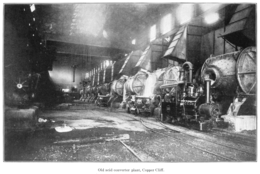
Manhès -David-processen är en förädlingsprocess av kopparstenen , uppfann 1880 av den franske industrimannen Pierre Manhès och hans ingenjör Paul David [ fr ] . Inspirerad av Bessemer-processen består den av användningen av en omvandlare för att med luft oxidera de oönskade kemiska elementen (främst järn och svavel ) som finns i mattan, för att omvandla den till koppar.
Mängden av de grundämnen som ska oxideras, liksom den låga värme som produceras av de kemiska reaktionerna , leder till drastiska modifieringar av omvandlaren. Manhès och David designade den som en horisontell cylinder, med munstycken riktade från ena änden till den andra. Några år senare fodrade de amerikanska ingenjörerna William H. Peirce och Elias Anton Cappelen Smith den med grundläggande eldfasta material, mycket mer hållbara än det som användes av de franska uppfinnarna. Även om denna förbättring inte förändrar principerna för processen, underlättar den dess utbredda användning, vilket påskyndar övergången av kopparproduktion från Storbritannien till USA.
I början av 2000-talet förfinade Pierce-Smith-omvandlarna [ fr ] 90 % av kopparstenen och används i 60 % av det utvunna nickelet . Denna omvandlare, liksom tillsatsen av rent syre, automatiseringen av driften, behandlingen av rök och den ökande storleken på verktygen, säkerställde hållbarheten hos Manhès-David-processen, även om moderna verktyg har liten relation med sina förfäder.
Ursprunget till processen
Relation med Bessemer-processen
Precis som järn som produceras av en masugn kommer ut legerat med andra kemiska grundämnen som gjutjärn, blir koppar som utvinns ur malm en legering med svavel, järn etc. som kallas matt. Att tillämpa samma reningsprocesser på dessa två metaller är därför logiskt. Att tillämpa Bessemer-processen på kopparmetallurgi föreslogs, och principen validerades 1866, tio år efter Henry Bessemers uppfinning, av den ryske ingenjören Semenikow.
Förfining av legeringen i omvandlaren är möjlig eftersom förbränningen av oönskade element är starkt exotermisk: oxidationen av kisel och kol producerar 32,8 respektive 10,3 kilojoule per kilogram. Å andra sidan, om en kopparsten innehåller ett överflöd av järn och svavel, måste dessa grundämnen först separeras (vilket förbrukar 6,8 kilojoule per kilo FeS) innan deras oxidation (som endast producerar 5,9 respektive 9,1 kJ/kg) kan börja .
Första försöken
De första förfiningarna av kopparlegeringar med en omvandlare ägde rum i Ducktown , Tennessee , där A. Raht arbetade med en partiell förfining av mattan från 1866 till 1875. 1867 försökte ryssarna Jossa och Latelin experimentellt verifiera studierna av Semenikow. 1870 avbröt de sina experiment efter att bara ha lyckats öka kopparhalten från 31% till 72-80%.
I England fortsatte John Hollway dessa rättegångar fram till 1878. Liksom sina föregångare observerade han att om blåsningen började på ett tillfredsställande sätt, blev det mer och mer intermittent allt eftersom förädlingen fortskred. Hindren han stötte på var många:
- Vikten av producerad slagg var lika med koppars och dess volym var mycket större än den i omvandlaren. Det var därför nödvändigt att tömma retorten regelbundet.
- Densiteten hos den smälta metallen förändrades kraftigt (med koppar som hade en densitet som var tre gånger så stor som den pyrit som den är gjord av).
- Varaktigheten av luftblåsningen, som kan uppgå till två timmar, innebar stora värmeförluster.
- Det kiselhaltiga eldfasta materialet absorberades av slaggen, i vilken det fungerade som flussmedel .
Alla svårigheter som man stötte på kunde inte lösas lätt: den termiska värmebalansen för förädlingsreaktionen i luft av koppar var inte lika gynnsam som för järn, och mattan stelnade i formorna innan den raffinerades. Även när den modifierades kunde en Bessemer-omvandlare i bästa fall ta bort järn och en del svavel. Hollway misslyckades, men genom att publicera alla detaljer om sina experiment identifierade han de väsentliga problemen.
Laterala tuyeres
På 1870-talet började den franske industrimannen Pierre Manhès sina första försök med en liten, vanlig Bessemer-konverter på 50 kg i sin fabrik i Vedène , sedan i fabriker i Éguilles , nära Avignon . Han försökte förädla en matta med 25 till 30 % koppar som tidigare smält i en degel. Men liksom Hollway lyckades han inte förfina matten helt. Oxidationen av oönskade element skedde som förväntat, men driften avbröts snabbt av uppkomsten av metallisk koppar. Skärsten, som var en jonisk förening, var oblandbar med slaggen, men också med den smälta metallen. Den senare, som är tätare (ρ koppar ≈ 9), gick till botten av omvandlaren och täppte till munstyckena.
Pierre Manhès patenterade sedan användningen av tillsatser vars oxidation skulle frigöra tillräckligt med värme för att undvika att fastna. Till slut var det fransmannen Paul David, då ingenjör i hans fabrik 1880, som föreslog lösningen. Han föreslog horisontella munstycken placerade på tillräckligt avstånd från botten av omvandlaren så att kopparn kunde samlas under dem och luften blåser konstant i mattan. År 1881 var deras omvandlare både tekniskt och kostnadseffektiv.
Hösten 1884 antogs processen i USA av Parrot Silver and Copper Company i Butte , Montana . De två typerna blev större och större och ökade från en kapacitet på ett ton till åtta ton 1912, och till och med femton ton för cylindriska omvandlare 1920.
Peirce-Smith-omvandlare i Washoe-fabriken i Anaconda Copper 1920. Kapaciteten är 65 ton kopparmatt, blåst på tre timmar (vit metall) + en timme fyrtiofem minuter (blister). Formen på omvandlaren är av typen Great Falls.
Förbättring av Peirce och Smith
Eftersom slaggen blir anrikad med järnoxid under reaktionen i luft, blir den basisk och förenas sedan med den kiselhaltiga eldfasta beklädnaden, som är mycket sur . Ett grundläggande eldfast foder skulle inte reagera och skulle därför sänka produktionskostnaden. Antagandet av ett foder inspirerat av ett som utvecklats av Sidney Thomas och Percy Gilchrist 1877 föreslogs av Hollway under hans senaste tester i början av 1800-talet. Idén testades dock inte, eftersom grundläggande problem relaterade till luftblåsningen var mer av ett problem än eldfast optimering.
År 1890 testades ett grundläggande eldfast foder på en av Parrot Smelters Manhès-David-omvandlare, i Butte, under ledning av Herman A. Keller. Testerna resulterade inte i ett foder som var kompatibelt med industriell drift. 1906 lyckades Ralph Baggaley, fortfarande i Montana, efter ett antal tester, med att industrialisera en grundbeläggning vid Pittsmont Smelter, som övergavs 1908 efter att han lämnat fabriken. Efter allt detta lyckades norrmannen Kudsen från 1908 använda en grundbeläggning med Sulitjelma-gruvorna . Han utförde två på varandra följande blåsningar där, först i en liten konverter med en basisk beläggning, och sedan i en andra traditionell konverter med en sur beläggning.
Slutligen, 1909, vid Baltimore Copper Companys smältverk, lyckades amerikanerna William H. Peirce och Elias AC Smith ta itu med de huvudsakliga nackdelarna med grundläggande eldfasta material; grundläggande eldfasta material var ömtåligare och framför allt avledde de mer värme än sura eldfasta material. Genom att utveckla ett murverk lämpligt för den cylindriska omvandlaren och öka mängden metall som matas in i ugnen löste de de återstående problemen.
Peirce och Smiths omvandlare visade sig vara mycket fördelaktigare än Manhès och Davids. Det grundläggande eldfasta materialet, som inte reagerade med slagg, höll mycket längre. Denna förbättring eliminerade behovet av utbyte av omvandlare, konstruktion av murverksinstallationer och utbytesomvandlare (det fanns två murverksomvandlare för varje i tjänst 1897 på Anaconda Copper ). Det minskade också risken för piercingar på grund av dålig kontroll över slitaget av det eldfasta materialet. Det eldfasta skiktet kan då vara tunnare, vilket ökar omvandlarens kapacitet. Kapaciteten var inte beroende av slitage av det eldfasta materialet, vilket förenklade hanteringen av flöden av smält metall i fabriker.
Om materialet som används för att förbereda det sura eldfasta materialet innehåller koppar, eller till och med silver eller guld (ofta förknippat med koppar i guldhaltig kvarts ), förenas dessa metaller med mattan när fodret tas bort. Med tanke på det eldfasta materialets snabba förstörelse realiseras därför den ekonomiska fördelen med ett surt eldfast material endast om dess förbrukning tillför ett värde till processen. Denna situation är dock ganska sällsynt och även om så är fallet kan kiseldioxid rik på ädelmetaller framställas på andra ekonomiskt lönsamma sätt. År 1921 ansågs därför det grundläggande eldfasta materialet vara huvudfaktorn i kostnadsminskningen vid utvinning av kopparmalm. I vissa fall rapporterades en minskning av konverteringskostnaderna från 15–20 USD till 4–5 USD.
Konvertering inom kopparmetallurgi
En blandning av koppar- och järnsulfider, kallad skärsten, behandlas i omvandlare för att oxidera järn i det första steget och oxidera koppar i det andra steget. I det första steget blåses syreberikad luft genom munstyckena för att delvis omvandla metallsulfider till oxider:
- FeS + O 2 → FeO + SO 2
- CuS + O 2 → CuO + SO 2
Eftersom järn har större affinitet till syre, reagerar den producerade kopparoxiden med den återstående järnsulfiden:
- CuO + FeS → CuS + FeO
Huvuddelen av kopparoxiden omvandlas tillbaka till formen av sulfid. För att separera den erhållna järnoxiden flussmedel (huvudsakligen kiseldioxid) i omvandlaren. Kiseldioxid reagerar med järnoxid för att producera en lätt slaggfas , som hälls av genom huven när omvandlaren lutas runt rotationsaxeln:
- 2 FeO + SiO 2 → Fe 2 SiO 4 (ibland betecknad som 2FeO•SiO 2 , fayalit )
Efter att den första portionen slagg har hällts ut från omvandlaren, tillsätts en ny portion skärsten, och omvandlingsoperationen upprepas många gånger tills omvandlaren är fylld med den renade kopparsulfiden. Omvandlarslaggen återvinns vanligtvis till smältsteget på grund av det höga innehållet av koppar i denna biprodukt. Konvertergas innehåller mer än 10 % svaveldioxid, som vanligtvis fångas upp för produktion av svavelsyra .
Det andra steget av omvandlingen syftar till att oxidera kopparsulfidfasen (renad i det första steget) och producerar blisterkoppar . Följande reaktion sker i omvandlaren:
- CuS + O 2 → Cu + SO 2
Kopparhalten i den erhållna blisterkopparn är vanligtvis mer än 95 %. Blisterkoppar är slutprodukten av konvertering.